Go back to News
Simple Steps to Clean up a Huge Environmental Issue
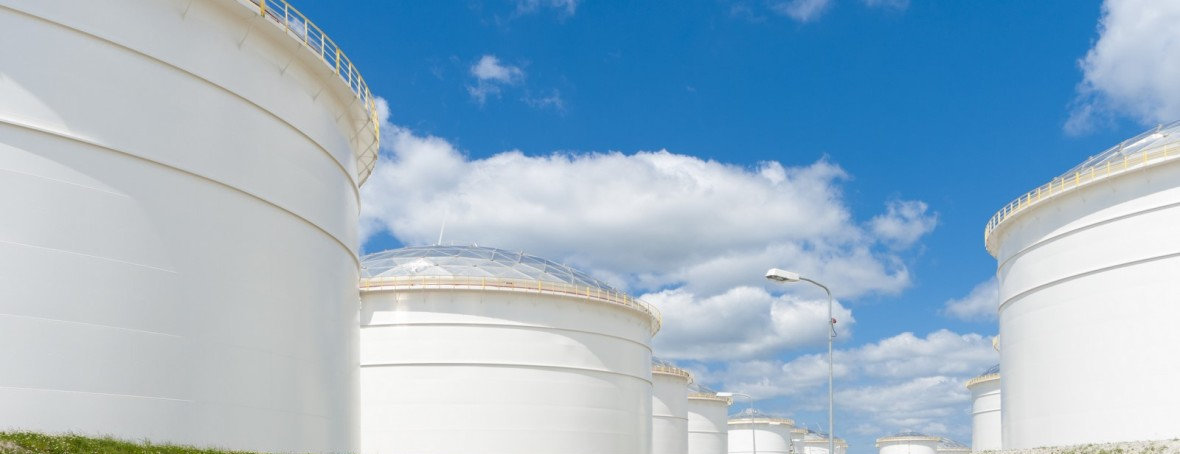
Most of the UK population live in towns and cities and often cheek by jowl with industrial activity including bulk chemical/petrol storage and biogas generation.
We are lucky to have a legal infrastructure that ensures all UK operators follow strict safety and environmental guidelines intended to keep us safe.
But there is always room for improvement. We passionately believe that huge reductions in emissions from tank farms can be achieved using the best available techniques and reference to international standards.
The speed of change and increasing rate of adoption of new, cleaner technologies is literally breathtaking as we all wake up to the damage we have inflicted on our world.
Assentech has been developing techniques to measure and reduce emissions from tank farms for over a decade. The key is keeping volatile compounds inside the tanks but allowing them to breathe when required such as filling/emptying and fluctuations in temperature. At all other times, a breather valve should remain closed with minimal leaks.
These valves have immense flow capacity so if not functioning or set correctly can leak hundreds of tons of invisible GWP emissions into the atmosphere.
Two international standards regulate the design, application and production of breather valves. These are ISO28300 and API2000. Both standards have specified maximum leak rates for all production vents, i.e. 0.014m³/h for vents up to 6”. The shame is that only 2 out of the 20 worldwide manufacturers test to this standard. This ultimately has led to a huge problem with the majority of breather valves that are installed at facilities are not leak-tight and will allow huge volumes of vapour to release into the atmosphere.
With over 1500 sites in the UK having more than 10 storage tanks with capacity ranging from 10 to 8000 tonnes of flammable or toxic liquid the potential for leakage is immense.
In a recent case study on a biogas plant, we recorded annual emissions of 161 tonnes of global warming potential from each valve installed. This is equivalent to 112 double-decker buses by volume per year.
We reduced this huge volume of leakage down to 159kg per year which is approximately the same as 10% of one double-decker bus.
So we saved the customer £5,655 in lost methane and an incalculable value to our environment. This was a true win/win deal.
Our simple advice is to ensure that End Users, Regulators, and Insurers insist on a valid individual leak test certificate on both vacuum and pressure ports for all the breather valves purchased, installed or serviced.
We would recommend that these assets are inspected yearly and given a full service at intervals no longer than 3 years. Adhering to the best available practices and careful due diligence of your supplier will ensure global emissions are substantially reduced.
Contact us
If you would like to place an order or find out more, please email info@assentech.co.uk, call on +44 1726 844 707, or fill in a contact form here.