Shifting from Tanker Top Loading to Tanker Bottom Loading
For Safer, Cleaner and More Efficient Loading Operations
As operations at liquid storage terminals have evolved, so have the ways in which the vessels that transport the commodities stored there are loaded. Traditional loading of tank trucks, transport trailers and railcars in liquid terminals occurred from the top of the transport vessel, with terminal personnel required to climb to the top of these devices in order to initiate and carry out the loading process. This type of loading brings with it a unique set of concerns, both in terms of safety and potential environmental impact. The simple act of ascending to the top of the tank trailer or railcar carries potential safety issues, as the personnel tasked with this job face the risk of injury due to falls. Top loading also requires the use of expensive loading gantries, racks and loading-arm equipment.
With all of this said, top loading of transports and railcars can still be a safe, efficient and cost- effective method of product loading in many situations, but many terminal operators have begun implementing a loading process that has proven to be safer, faster and more efficient than traditional top-loading operations. This method is called bottom loading.
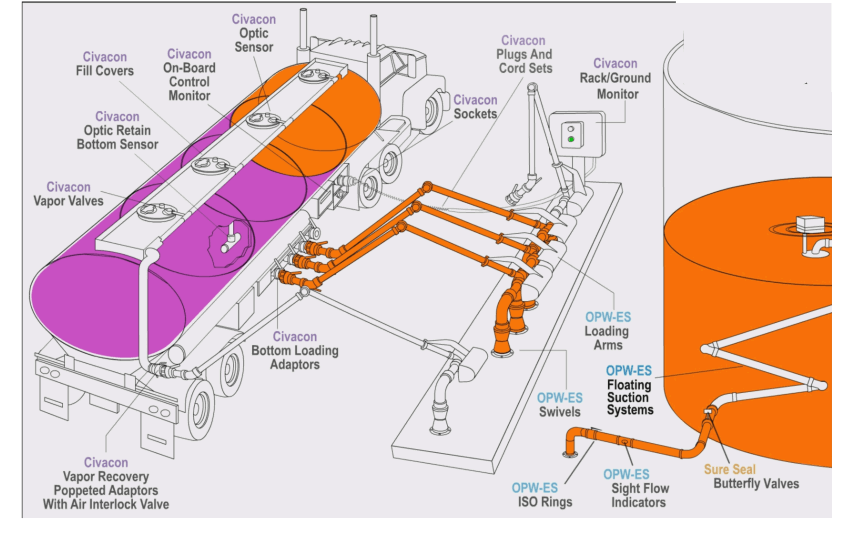
The advantages of bottom loading are many. The most obvious is safety. Employee operators are no longer required to climb to the top of the transportation vessel in order to complete the loading process. Also because bottom loading occurs in a closed-loop arrangement, the chance of static electricity buildup causing a fire or explosion is greatly reduced since the potential for a fuel- oxygen mixture is reduced. Operators have no need to open a large hatch on the truck and release large volumes of vapor to the atmosphere. When bottom loading equipment is installed correctly, the desired level of near-zero vapor emissions can be achieved.
Operationally, advances in bottom-loading equipment have also made it more ergonomic and less physically taxing on the loader. This is less taxing on the operator while benefiting the terminal in the form of speed. Bottom loading also allows for the simultaneous loading of several tank compartments at the same time, which increases the speed and efficiency of product loading.
In a nutshell, safer, more ergonomic and faster loading is what bottom loading is all about.
Bottom-loading islands are simpler and cheaper to build than top-loading racks. This leads to safer loading in a shorter period of time with less chance of spillage and vapor loss. Specific benefits of bottom-loading systems and equipment from OPW Engineered Systems include:
- Safer working environment and reduction of your environmental impact by reducing the emitted vapors, with the capability to fully recover any vapors that may escape.
- Increased safety for the person operating the loading arm since that person remains on the ground and is no longer required to climb to the top of the vehicle, where falls can occur.
- Loading-arm connections to the vehicle are made more quickly so overall loading time is reduced.
- The creation of less turbulence in the tank, reducing the danger associated with the generation of static electricity.
- Faster tank filling, with a number of compartments able to be loaded simultaneously.
These characteristics make the bottom-loading equipment supplied by Assentech and manufactured by OPW Engineered Systems ideal for any type of terminal-loading application.
Please Contact us if you would like to know more about how Assentech can help you in the conversion from top loading to bottom loading.
We supply a broad range of loading equipment and complete loading platforms, gantries and racks.
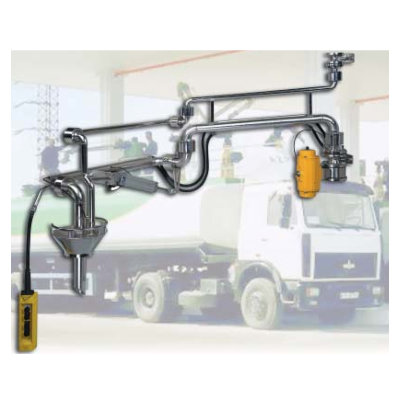
Vapour Recovery Arms
Contact us
If you would like to place an order or find out more, please email info@assentech.co.uk, call on +44 1726 844 707, or fill in a contact form here.